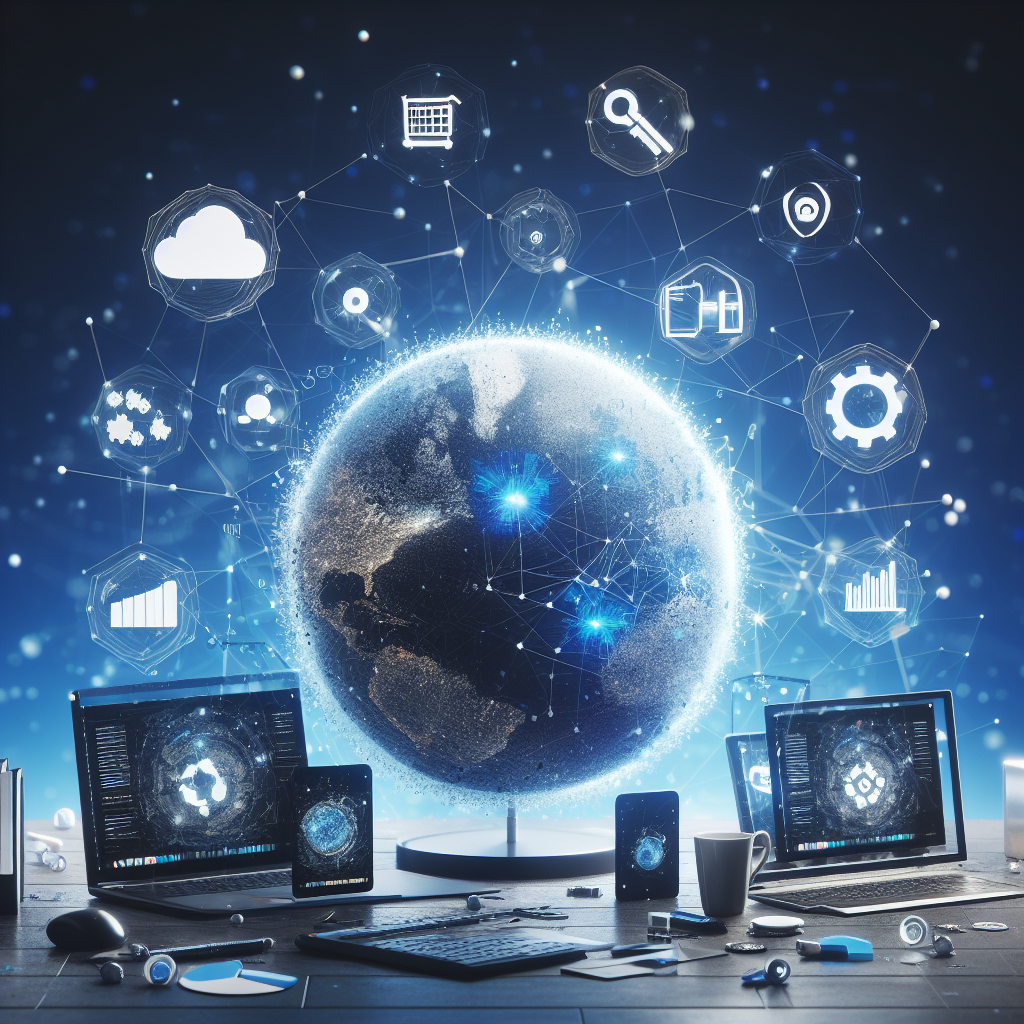
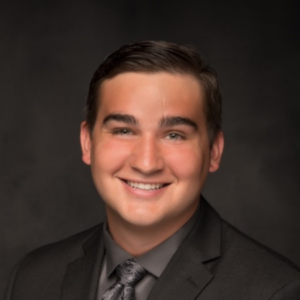
Chris Warren
Forum Replies Created
-
Chris Warren
MemberApril 24, 2024 at 10:51 am in reply to: Moving cost from an expense account to a production order::One option would be to make your packaging material an item, and then consume it in the production order. This is how we’ve done it for a lot of our products.
Another option would be to do a revaluation of the item after the production order is finished, making sure that the inventory revaluation account is set to that expense account in the General Posting Setup.
Apart from that, I’m unaware of another way to add a ‘charge’ to a production order.
-
::
While it’s not a report to compare all production orders, have you checked out the “Statistics” tab on a Released or Finished Production order? It sounds like this would show you the information you’re looking for.
We’ve used this during financial audits to prove our costing methods for our Items/Work Centers/Machine Centers. I’ve also managed to recreate this in PowerBI and Jet Reports to get the report that you’re looking for in a single spreadsheet, since I have yet to find an OOTB report from NAV/BC that can do this.
-
Chris Warren
MemberApril 4, 2024 at 4:33 pm in reply to: Cannot finish line 10000 on production order -
::
This is an interesting one.
How do you determine what your total demand is vs. what you can manufacture? Do you have a sales order open in BC that shows shipped vs. requested quantity? Are you using any of the demand capabilities inside of BC? If not, I’m not sure there’s an easy way to pull a report like this since BC won’t know what you were attempting to sell vs. what was in inventory.
-
Chris Warren
MemberMarch 26, 2024 at 8:17 pm in reply to: Summit Call For Speakers and Session Topics::Thanks. I submitted two today and only had issues when submitting a second session—it refreshes the page and gives you a message at the top requiring you to submit the form a second time. The message isn’t too clear, but it seems like it went through.
To click submit, you must upload your photo and company logo a second time to receive the confirmation email.
-
-
-
::
Ah… this brings back a lot of ‘fun’ memories I had when I took over our NAV instance 6-7 years ago.
We had a very similar situation, where we needed to change practically all of our item tracking codes. Some items weren’t tracked that needed to be, and other items (think screws, nuts, washers) were item tracked and no one knew why.
@Lewis_Rosenberg Is correct with what he said. But we didn’t want to create all new item cards, and essentially have duplicates in the system with one being item tracked, and the other not. So we had our Partner write a report that would update the item tracking code using the process that Lewis mentioned. But there are a lot of things to take into account:
- You have to bring that item to zero quantity for this to work
- Before you bring the item to zero, run an Inventory Valuation Report.
- Do an item journal to bring the inventory to zero
- Run the report on that item to update the tracking
- Put the item back in using an Item Journal with all respective lot or serial numbers
- Run “Adjust Cost – Item Entries”
- Run an Inventory Valuation to ensure your Inventory Value didn’t change
- Perform a revaluation if necessary to get it back in balance.
And if you are using Warehousing, you will want to ensure your warehouse location is set up to your liking. There is a setup that you need to enable if you want to track at the Zone/Bin level. Otherwise, it just shows what lots/serial are at a location, and not where each lot/serial can be located within the warehouse.
It took me a week with 4-5 people to get our inventory straight with the proper item tracking and ensure it didn’t mess up our financials. We now have a process in place when we create items, we do an analysis of what actually needs to be tracked, so we don’t run into this issue again.
-
-
Chris Warren
MemberApril 24, 2024 at 10:30 pm in reply to: Moving cost from an expense account to a production order -
-
-
-
-
Chris Warren
MemberFebruary 8, 2024 at 11:36 am in reply to: Allow Customers to Enter Their Own Opportunity