Mastering the Distinctions Between Pegging and Reservation in Dynamics 365 Finance & Operations
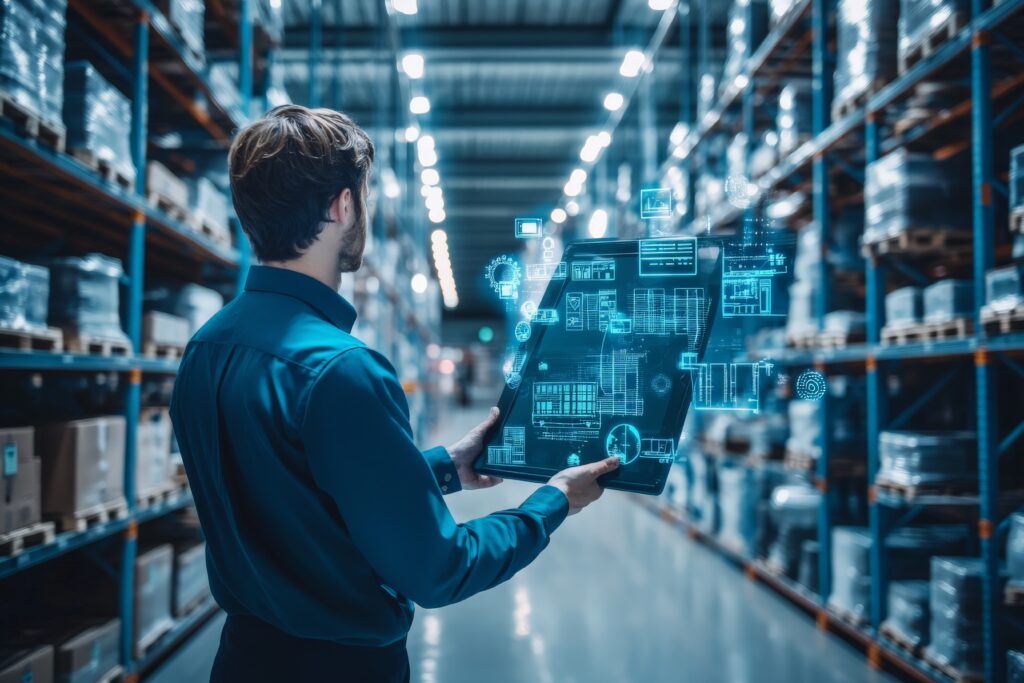
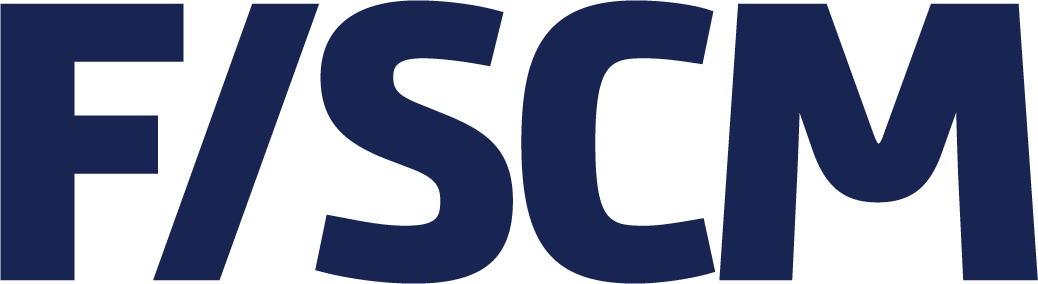
In Dynamics 365 Finance & Operations (D365FO), inventory management strategies include two critical processes: pegging and reservation. Although these concepts may appear similar, they serve distinct purposes and have unique characteristics. A clear understanding of these differences will help D365FO users make informed decisions about managing supply and demand effectively.
What Is Pegging?
Pegging is a function within master planning, designed to link supply (planned or firmed orders) with demand (such as sales orders or production requirements). It provides a clear picture of how the system intends to cover demand, but it does not physically reserve or allocate inventory. Instead, pegging is flexible and dynamic, adjusting with each master planning run based on updated requirements. Key characteristics of include:
- Created by master planning: Itās generated automatically during planning runs.
- Links supply to demand: It indicates which supplies will likely fulfill which demands.
- Updates dynamically: It adjusts during each planning run as requirements evolve
- Does not reserve inventory: It represents a plan, not a commitment of physical inventory.
To better understand pegging, hereās an example: A sales order is placed for 100 units of Item A with a ship date of January 31. During the master planning process, the system generates a planned purchase order for 100 units of Item A, due by January 28, and pegs it to the sales order. This pegging shows the intended supply to meet that demand but does not commit the inventory.
What Is Reservation?
Reservation, in contrast, involves the actual allocation of inventory to specific demands. It is a more definitive process than pegging, permanently setting aside physical or ordered inventory to ensure the demand is met. Reservations can be created manually by a user or automatically based on system settings and configurations. Key characteristics of reservation include:
- Manual or automatic process: It can be initiated by a user or configured to occur automatically during order entry or processing
- Allocates inventory: It dedicates specific physical or ordered inventory to a demand.
- Permanent allocation: It requires manual intervention to modify once set.
- Reduces available inventory: It affects available stock by reserving items for exclusive use.
Here is an example of a reservation: A customer places an order for 50 units of Item B. To ensure fulfillment, a manager manually reserves 50 units from the available stock. This process earmarks the inventory, preventing its use for any other purpose until the order is completed.
Pegging vs. Reservation
Pegging | Reservation | |
---|---|---|
Purpose | Focuses on planning and demand forecasting | Ensures specific inventory is set aside for real demands |
Timing | Occurs during master planning runs | Can occur during order entry or later in the fulfillment process |
Flexibility | Highly adaptable, updating with each planning run | More rigid, requiring user intervention to adjust |
Impact on Inventory | Does not affect physical inventory availability | Reduces available inventory or reserves incoming stock |
Visibility | Reflected in master planning views and net requirements | Recorded in inventory transactions and on-hand inventory data |
How Pegging and Reservation Work Together
There are scenarios where pegging and reservation complement each other. For instance:
- A sales order is created for 200 units of Item C.
- Master planning runs, generating a planned production order for 200 units, pegged to the sales order.
- When the planned production order is firmed, the system automatically creates reservations based on the pegging information, allocating inventory to ensure fulfillment.
This interaction highlights how pegging enables effective planning, while reservation ensures inventory is secured when plans are converted into actual orders.
Why Understanding the Difference Matters
Mastering the distinctions between pegging and reservation empowers D365FO users to optimize their inventory management processes. Pegging supports strategic planning by linking supply and demand dynamically. Reservation guarantees inventory allocation for critical demands. Together, they form a comprehensive approach to managing supply chain operations, enhancing efficiency, and improving customer satisfaction.
By leveraging both pegging and reservation appropriately, inventory managers can find the balance between flexibility and commitment, ensuring smooth order fulfillment and effective supply chain management.
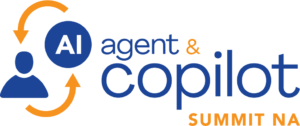
AI Agent & Copilot Summit NAĀ is an AI-first event to define the opportunities, impact, and outcomes possible with Microsoft Copilot for mid-market & enterprise companies. Register nowĀ to attend AI Agent & Copilot Summit in San Diego, CA from March 17-19, 2026.