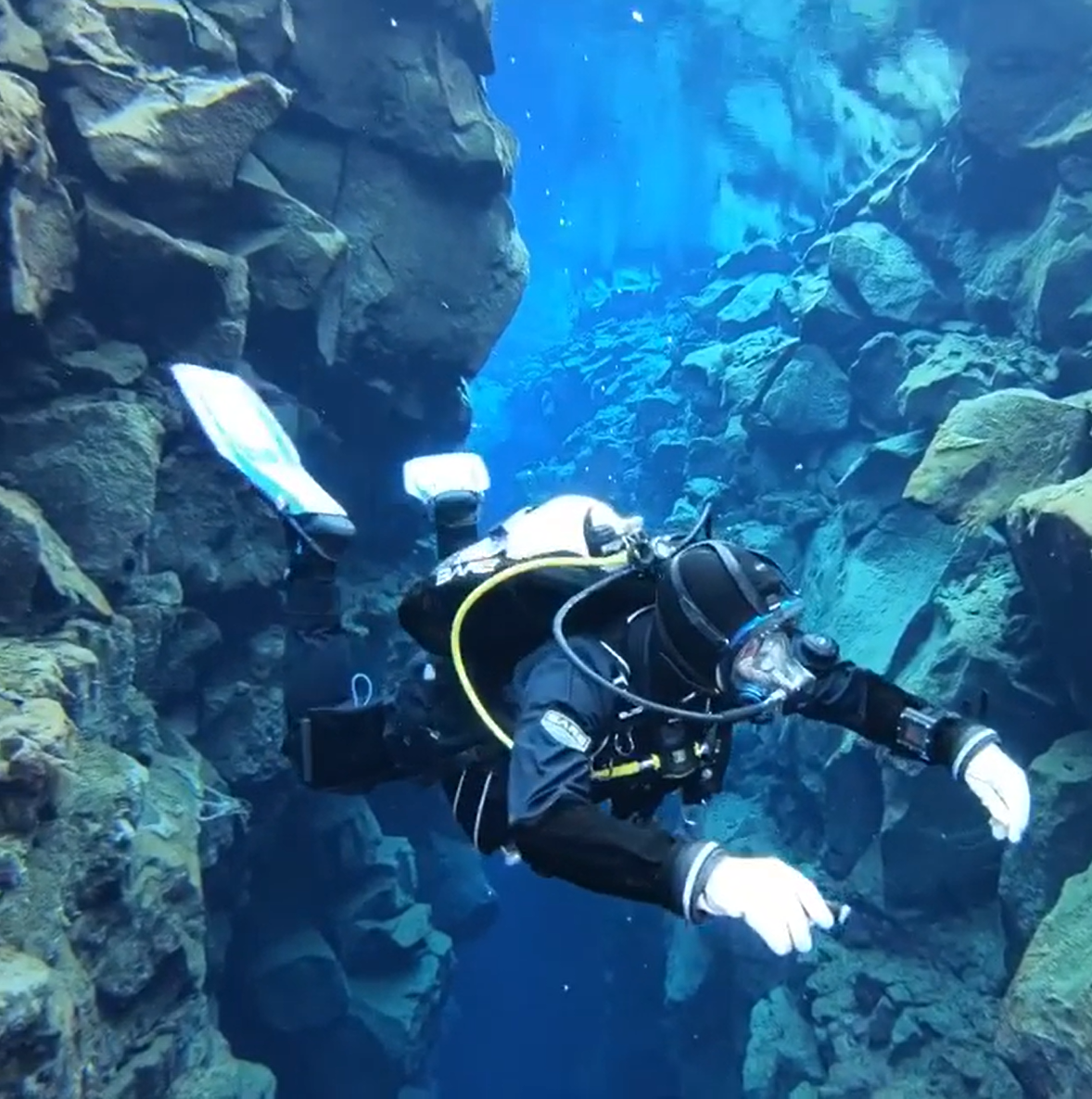
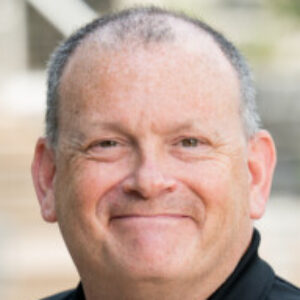
Steven Chinsky MVP
Forum Replies Created
-
Steven Chinsky MVP
MemberApril 28, 2025 at 11:16 am in reply to: Customer Setup – Best Practices BC::Lori – I normally number my customers beginning with a C and 4-5 digits. The number is irrelevant since I can search by Name, Phone Number, etc. As for Ship-to’s I number them by Zip Code and/or City Name.
If you want a way to search for Ship-to, I will expose the Ship-to List Page to all users so they can see the Ship-to’s.
One other note… Adding Avalara does not make me rethink changing my customer numbering. It will allow me to add a process to always validate Sell/Bill/Ship-to addresses using the Avalara address validation engine.
Hope this helps. Email of you have more questions.
Thank you,
Steve
-
Steven Chinsky MVP
MemberApril 23, 2025 at 10:58 am in reply to: Payment Method Code (with Balancing Account) and Bank Reconciliation::Leslie,
Since you noted Bank Reconciliation, have you linked the Bank Account so that you can import Bank Statements? If no, importing the Bank Statement (Daily, Weekly, Bi-Weekly, Monthly) will pull those payments into the Bank Rec, for Bank Statement Lines. The Finance Team can send the payment to a General Journal and post the application against the Invoice, while doing the Bank Rekonciliation. Then there is no timing issues since you are importing the Bank Statement and the application will occur on the date it processed at then Bank.
The Payment Method process is sweet since it clears the invoice and records the payment. If Finance wants to treat the payment on the actual day it occurs, consider linking the Bank and recording the transaction off the Bank Rekonciliation.
If you want to know more, reply back and I will send you a handout on Linking and Bank Rekonciliation importing the Bank Statement.
Steve – Microsoft MVP
-
::
@Ryan Boyce – BC CRM (Marketing and Relationship Management) is a great starting point for ‘old school’ beginners. It provides the following features:
1. Salespeople/Teams
2. Tasks/To-Do’s
3. Opportunities
4. Contacts
5. Campaigns
6. Questionnaires
Consider going into a Sandbox and trying it out. If you need more direction or want a demo, feel free to reach out.
Thanks,
Steve
-
Steven Chinsky MVP
MemberJanuary 31, 2025 at 5:27 pm in reply to: New v25 1099 Feature – How-To Handout (READ IT) -
Steven Chinsky MVP
MemberJanuary 31, 2025 at 5:25 pm in reply to: Insight Works – Shop Floor Insights -
Steven Chinsky MVP
MemberJanuary 31, 2025 at 5:23 pm in reply to: Fully Received/Invoiced POs not removed from Purchase Orders open/released list::Jodie – If I recall the Continia process, the Invoice comes in and it performs the 3-way match and creates a Purchase Invoice ‘getting’ the Posted Receipts associated with the Invoice. The post completes but, as you noted, you have the PO left in the list. This is true when using the Get function.
I recommend that you manually or you can run via a Job Queue, the Delete Invoiced Purchase Orders function. Try this manually and you will see the job will remove only fully invoiced PO’s from the list.
Hope this helps.
Steve
-
Steven Chinsky MVP
MemberJuly 5, 2024 at 12:52 pm in reply to: US Companies in CA Tenant – handling 1099 vendors::David,
I have had the same just backwards, meaning, I have had customers with US environment and had a Canadian operation and created a Company within. You can setup the Sales Tax, in the US Company and also setup that company to reflect USD and additional currency for CAD. Not sure if you are consolidating but that can be done in BC too.
If you want to chat, reach out.
Steve
-
::
Sean,
I would do a comparision on the 2 most active APPs and they have been in BC the longest:
USTPay – Merchant Services | U.s. Transactions Corp. (ustranscorp.com)
iSolutions – iSolutionsPayments.com
I have implemented both.
Steve
-
::
@debpeters Scrap Factor % on the Routing Line is defined as scrap in relation to an operation. BC has a scrap factor % field in the routing that can be used to define if an operation generates scrap. This will increase the required quantities for all the components that are used in the operation and all previous operations. It will also increase the capacity need for the operation and all previous operations. If you use this then linking the components to the operations using the routing link codes are important (otherwise all your components will have increased quantities).
When the production order is created the value of the Scrap Factor % field from the routing line is transferred to the Scrap Factor % field of the production order routing and the capacity need for the operation is increased accordingly. The related components quantities are also increased accordingly. A great example of why to use this is operations that have a certain
expected failure rate.Now Fixed Scrap Quantity on the Routing Line Scrap is related to an operation that has defined fixed scrap quantity. Dynamics NAV has a fixed scrap quantity field in the routing; it has the same effect as the scrap factor % but with the difference that it is specified in an absolute quantity instead of a percentage.
You set this up in the Fixed Scrap Quantity field on the routing. When the production order is created the value of the Fixed Scrap Quantity field from the routing line is transferred to the Fixed Scrap Quantity field of the production order routing and the capacity need for the operation is increased accordingly. The related components quantities are also increased accordingly. This could, for example, be used for operations on a machine that needs to be setup and tested on a few units before starting the run. Another common example is if you are doing some destructive testing on a certain quantity as part of the operation.
I hope this helps. Now one thing to note, if you intention is to solely scrap at the component level, then setting the Scrap % on the BOM is the best approach.
Thanks,
Steve
-
Steven Chinsky MVP
MemberApril 4, 2024 at 10:33 am in reply to: Web Service Request Limits BC23 On-premise::Chris – I am going to add a tech guru to this and a close friend. He started to ask me questions only you can answer about setting the service settings and separate service tier for ODATA. Meet Brad. I will let him jump into the questions.
Thanks,
Steve
Brad – All yours š
-
::
Jessie – What the upcoming BC 3 Amigos You Tube podcast coming out this week. It is on 2024 Wave 1 new functionality. You can also go here: https://learn.microsoft.com/en-us/dynamics365/release-plan/2024wave1/smb/dynamics365-business-central/
Steve
learn.microsoft.com
Overview of Dynamics 365 Business Central 2024 release wave 1
Overview of Dynamics 365 Business Central 2024 release wave 1
-
Steven Chinsky MVP
MemberApril 3, 2024 at 9:28 am in reply to: Sales Forecasting in Business Central::Chris – Predictive or Historical Sales Forecasting I normally turn to 3 APPs: 1) Microsoft <b style=”font-family: inherit; font-size: inherit; color: var(–bb-body-text-color);”>Sales and Inventory Forecast. Yes Microsoft has one not used a lot and uses Cortana and AI to predict and history. 2) StockIQ I have used several times now. 3) AGR
If you need names to call StockIQ or AGR tell me.
Thanks,
Steve
-
::
Jonathon – Here is my developers reply as a sample…
If you have a flowfield and you want the drilldown to show a different set of data you can write code in the ondrilldown trigger.
This example has a flowfield for the sum of the Item quantity, but if you drill down ā youāll get the sales orders. I didnāt do anything but filter on the order, but you can see how it is as an example. This is a basic sample based on what I understand is the ask. It may be done differently with different requirements.
table 50100 “DEV New Table”
{
Caption = ‘New Table’;
DataClassification = CustomerContent;
fields
{
field(1; “Item No.”; Code[20])
{
Caption = ‘Item No.’;
TableRelation = Item;
}
field(15; “Quantitiy”; Decimal)
{
CalcFormula = sum(“Item Ledger Entry”.Quantity where(“Item No.” = field(“Item No.”)));
Caption = ‘Quantity’;
DecimalPlaces = 0 : 5;
Editable = false;
FieldClass = FlowField;
}
}
keys
{
key(PK; “Item No.”)
{
Clustered = true;
}
}
}
page 50100 “DEV New Page”
{
ApplicationArea = Basic, Suite;
Caption = ‘New Page’;
Extensible = false;
PageType = List;
SourceTable = “DEV New Table”;
UsageCategory = Lists;
layout
{
area(Content)
{
repeater(DevControl1)
{
field(Item_No; Rec.”Item No.”)
{
}
field(Quantitiy; Rec.Quantitiy)
{
trigger OnDrillDown()
var
SalesHeader: Record “Sales Header”;
begin
SalesHeader.SetRange(“Document Type”, “Sales Document Type”::Order);
Page.RunModal(Page::”DEV Sales List”, SalesHeader);
end;
}
}
}
}
}
page 50101 “DEV Sales List”
{
ApplicationArea = Basic, Suite;
Caption = ‘Sales List’;
Editable = false;
Extensible = false;
PageType = List;
SourceTable = “Sales Header”;
UsageCategory = None;
layout
{
area(Content)
{
repeater(DevControl1)
{
field(DocumentType; Rec.”Document Type”) { }
field(No_; Rec.”No.”) { }
field(ExternalDocumentNo; Rec.”External Document No.”) { }
}
}
}
}
Thanks,
Steve
-
::
@debpeters – Based on your scenario, if my BOM states I am to consume x quantity for $105 but I actually post consumption at $85 dollars worth, this would create a Variance (Favorable). Here is an attached flow I did in CRONUS.
Steve
-
::
@debpeters If you are looking to apply against components (Raw Materials) only, then I would use the Production BOM Scrap %. This way you are always pulling x% more than the stated Quantity per for the components. As for MRP, scrap % effects the expected quantity required for a Production Order and therefore is used in the planning engine. Your last statement about Standard Cost, if your Costing Method is Standard Cost and you have the Production BOM reflecting a Scrap%, when you rolled the Standard Cost the additional item cost will be included.
Hope this helps.
Steve