Using Dynamics 365 Business Central to Enhance the Cycle Counting Process
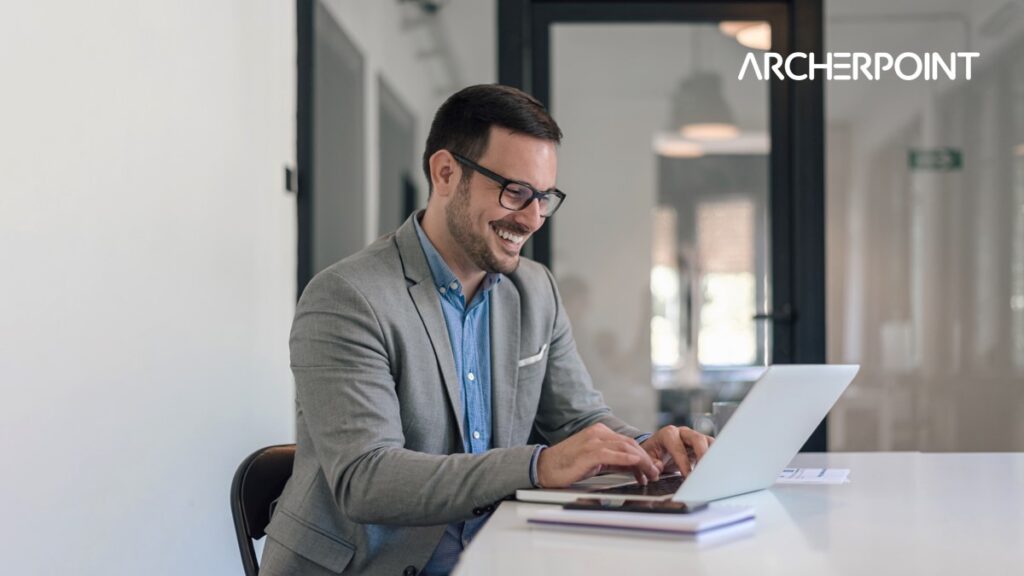
In the past, all operations and functioning of a business or warehouse had to be shut down to tally up the inventory. The inventory process was performed by hand, using an offline paper trail that completely disrupted business operations and was prone to human error.
Cycle counting is a technique that can be employed by businesses to precisely keep up with inventory. Using cycle counts requires splitting up all relevant inventory into multiple small groups. One or more employees count up each of these separate groups in a few days. To keep inventory statistics current, each subgroup is counted multiple times yearly.
By using cycle counts, a small group of employees can count the inventory of subgroup each day in a week, or as frequently as they need to, depending on the warehouse or business needs. The group of employees opts for a different subgroup each time they count, until they have gone through the whole inventory. Homing in on the root cause of an inventory count discrepancy becomes more straightforward when using cycle counts, ultimately helping to avoid having out-of-stock or overstocked items. Furthermore, by implementing cycle counts, businesses can increase their customer satisfaction, streamline operations and decrease overhead.
Bin Counting vs. ABC Counting
Although there are many different methods of cycle counting, the two main cycle count methods are Bin Counting and ABC Counting.
The Bin Counting method requires splitting up the warehouse areas into various sections, or bins, and then counting a specific number of these bins during each inventory run.
ABC counting, on the other hand, is grounded in the Pareto Principle, otherwise known as the ā80/20 ruleā. Using this method, low value items or items that are in lower demand are counted less frequently ā perhaps annually, while high turnover or high demand stock is counted more often. Medium value items are counted less often, such as a few times each year.
Core considerations for successful cycle counts
To ensure that the cycle count process is working optimally for your business, it is important to adhere to the following key principles:
- Keep a routine. It is crucial to carry out your counts on a regular schedule, whether you decide to carry them out once a year or multiple times a week. If your team is counting irregularly, this can lead to inaccurate figures, resulting in out-of-stock and overstock items, especially if the item is high through volume.
- Keep with your established methodology. Once you have decided on your counting methodology, establish a clear protocol for employees to count the same way each time. This will ensure clear and accurate inventory counts.
- Train all employees thoroughly. To properly implement your counting protocol, you will need to properly train each employee how to count. This can help avoid discrepancies in stock.
- All items count. Even for items that are slow moving, you need to keep track of them. Be sure to count all subgroups at least once a year, or within an appropriate timeframe.
- Root cause inventory discrepancies. Cycle counting allows companies to quickly identify where there are item discrepancies, so that they can identify what exactly is causing the problem. By avoiding reconciling discrepancies, such underlying problems can persist or even become exacerbated.
Put your time and money in automating the process. Having your employees carrying out the cycle counting process by hand is expensive, prone to error, and can take long periods of time. Investing in an automated solution that integrates with your WMS and ERP can streamline the process and reduce your overhead expenses.
How to use Dynamics 365 Business Central for cycle counts
Users can leverage Dynamics 365 Business Central to optimize their cycle count processes and maintain up-to-date inventory management. Business Central supports defining frequency and cycle count codes, picking out the subgroup to be counted, and providing input for manual counting or automated counting that uses barcodes or QR codes and scanners. Users can also use Business Central to assess cycle count execution, update inventory quantities and document the respective reasons for doing so.
Aside from Business Central, your company could gain a competitive edge by implementing applications designed to further enhance cycle counting. Solutions such as the Cycle Count Scheduler by Insight Works provide further reporting, scheduling and automation tools.
Work with a partner who knows Business Central and inventory management
The effectiveness of the technology your business is using ultimately depends on its implementation. By contacting ArcherPointās inventory management experts, your organization can explore the advantages of Business Centralās cycle count functionality and enhance it further. They can analyze your supporting systems and existing processes, identifying key areas where your business can improve.