Advanced Warehousing Meets Manufacturing: Dynamics for Manufacturing with Advanced Warehousing Processes
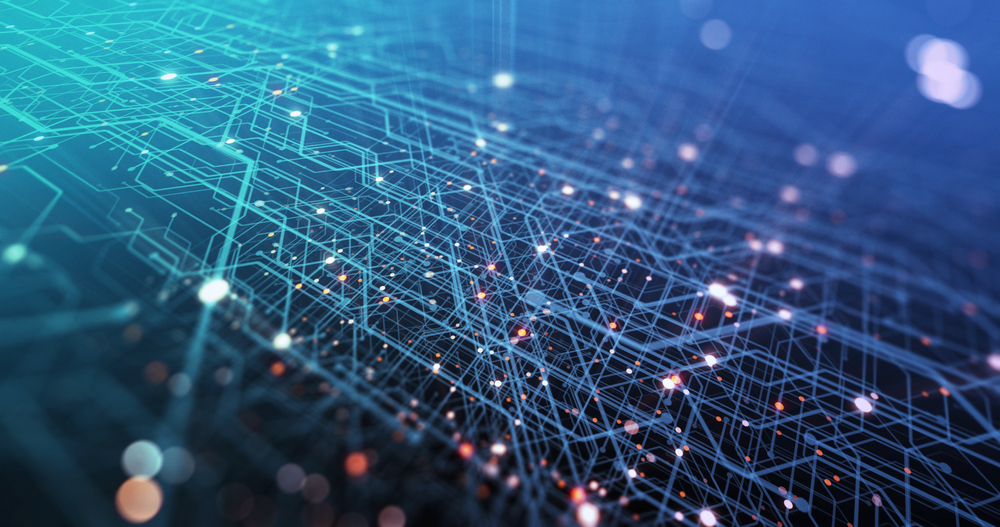
The current version of Microsoft Dynamics 365 offers a warehouse management system (WMS) module that competes with Tier 1 WMS systems and is fully integrated with built-in manufacturing functionality. Whether a business is discrete manufacturing, process manufacturing, Lean manufacturing or a combination of all three, Dynamics 365 for Manufacturing offers a flexible solution to run operations. When determining how to proceed, the business can implement a simple solution using Basic Warehousing functionality or implement the out-of-the-box fully mobile-capable Advanced Warehousing solution in D365 for their manufacturing environment.
During the project, design decision-makers will need to determine the best configuration to support the business processes that are being implemented. The decision-makers may want assistance from their consulting partner in determining what relevant functionality exists within the system and what the best path forward is to satisfy their business requirements.
Below are some quick tips and tricks regarding functionality in the Dynamics warehouse management module that will help optimize the business’ manufacturing and warehousing operations.
Leverage Resources
Resources can be configured with an input and output location to direct where raw materials will be consumed per operation step and where finished goods will be produced. Here are some advantages of implementing input and output locations:
- Define where raw materials will be consumed
- Inventory visibility at a resource location
- Improved real-time visibility of on-hand inventory and where it is at that moment
- Reduced reliance on tribal knowledge related to where raw material inventory will be or have been stored
- Guide sub-assembly feeder materials to parent production order(s)
- Sequence higher priority inventory to be put away first
Leverage Work Policies
Work policies can be configured to restrict when finished goods, co-product, or by-product put away will be completed. This allows the system to be configured to reduce the number of systemic and physical steps that need to be completed in an item’s lifecycle. Below describes how these can be used to optimize business processes:
- Immediately make sub-assembly inventory available for parent production order
- Eliminate unnecessary data entry of movement of sub-assembly inventory to parent production order
- Configuration is warehouse-, location-, and item-specific, so it can be rules-based
- The receipt of a sub-contract purchase order can drive the report as a finished process automatically