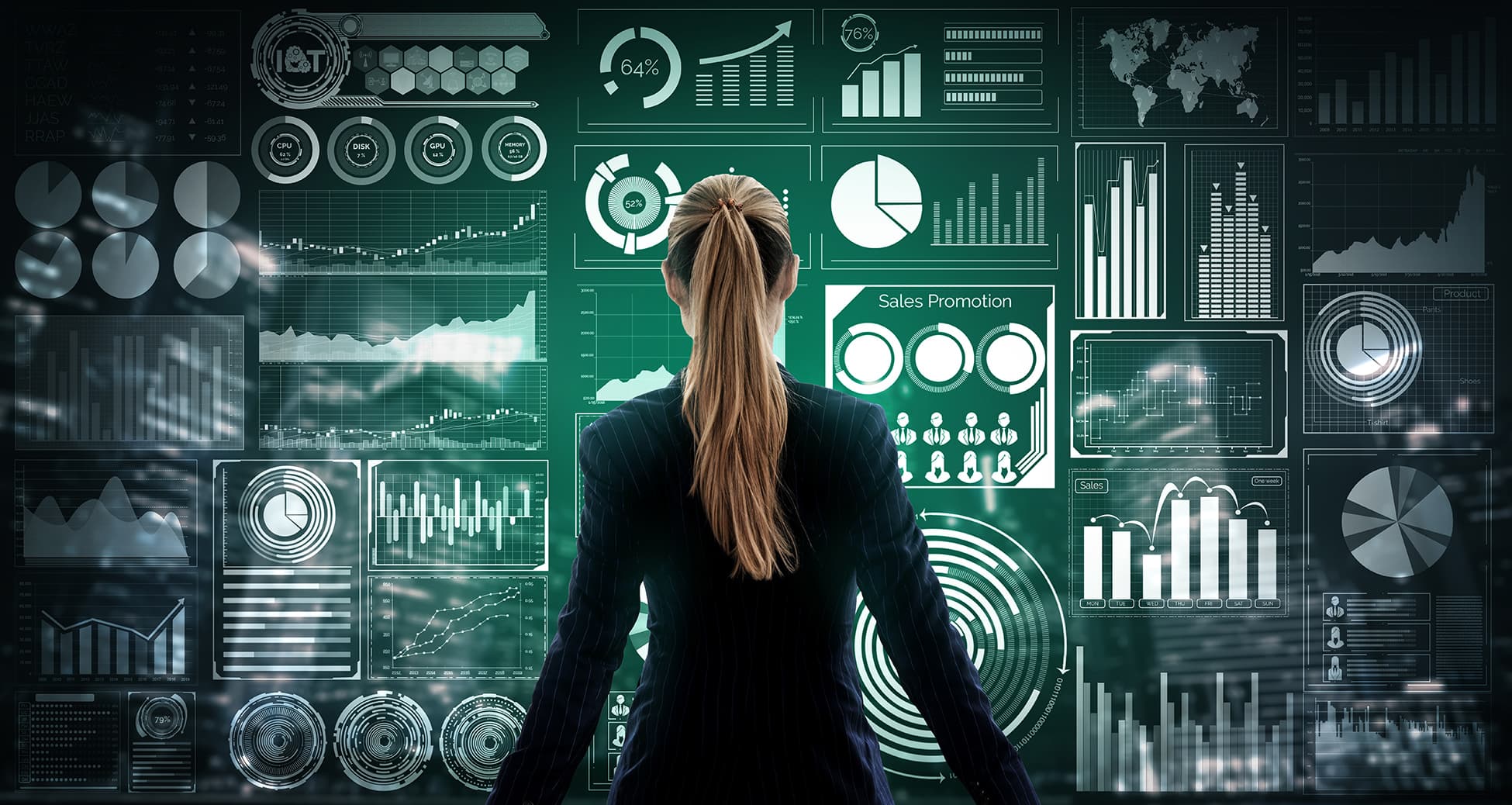
Lot no. changes
-
Lot no. changes
Posted by DSC Communities on December 21, 2016 at 4:11 pm-
Kris Ruyeras
MemberDecember 21, 2016 at 4:11 PM
Hello All,
I’m looking to see how others are doing or best practice on Lot No. changes or movement? Example is when an item was brought in with the incorrect Lot No. They would need to change the Lot No. to the correct one and at times expiration dates.
There’s a process here but I want to compare how others are doing so.
——————————
Kristoffer Ruyeras
Director of Business Technology
Bellegrove Medical Supply
Redmond, WA
—————————— -
You can use the item reclass journal to change the lot number. Enter the item number, location, quantity, etc. on the line. Then go into the item tracking lines and you can find Lot No. and New Lot No. fields. Enter the current and new lot numbers and then quantity and then post. In the item ledger entry, you will see the reduction of the old lot number and the addition of the new lot number. You could also try reversing the receipt and re-receive with the correct lot numbers. Short of changing lot numbers at the sql table level (very dangerous), I don’t know of any other way.
——————————
Dave Wiser
Controller
Beckwith & Kuffel
Seattle WA
————————————————————————- -
Ian Ray
MemberDecember 21, 2016 at 6:30 PM
Item reclass or reverse receipt as above.
The other situation I’ve run into is needing to reverse an already consumed lot in a production order (or orders). I’m not sure if this counts as “best practice…” In this situation, I have negatively adjusted the output of the production order(s) to balance out all costs, positively adjusted the quantity of ingredients used, invoiced the errant purchase order, and applied a purchase credit memo to the bad purchase order line. Then, a corrected purchase order was entered, received, and I used the data from the old production orders to remake the production orders and output.
In my case, this was because QA data was attached to the lot which was in turn attached to the cost of the purchase. If this was not the case, once the ingredient was positively adjusted, it could have been changed with an item reclass without redoing purchasing.
The reason I go through this is when I have tried to do this in a test environment without unwinding all the steps, item tracing becomes polluted with the bad lot. I would be open to a better way that I am not aware of, especially considering the time involved in undoing several steps of production just to correct one typo on a PO.
——————————
Ian Ray
Cypress Grove Chevre
Arcata CA
————————————————————————- -
Building on the comments from Dave and Ian, it also depends what has happened with the Item (with the bad lot no.). That is, if it is caught early before it used the undo receipt or the reclass journal are perfect. If it caught later (after it has shipped or used in production), then you need to determine the what additional steps you want to talk inside NAV and what non-conformance info you want to record about the lot.
——————————
Andrew Good
President
Liberty Grove Software
Oakbrook Terrace IL
————————————————————————- -
One more thing to add, beware of just negatively adjusting out the bad and positively adjusting back in the good without applying the entries to one another. You want to maintain the item tracing ability from usage back to source if that is required for you.
——————————
Dave Wiser
Controller
Beckwith & Kuffel
Seattle WA
————————————————————————- -
Kris Ruyeras
MemberDecember 22, 2016 at 12:15 PM
Thanks everyone for the feedback. I knew Item reclass was the best approach and what I noticed in here, they’ve done lot changes by using Item adjustments going through positive and negative in which I’ve ask them it may not be the best approach.
This discussion validates that. Thank you all for the help!
——————————
Kristoffer Ruyeras
Director of Business Technology
Bellegrove Medical Supply
Redmond, WA
————————————————————————- -
Ian Ray
MemberDecember 22, 2016 at 12:29 PM
What Dave is saying about Item Tracing is absolutely correct. While I alluded to this a bit, if you do consume the incorrect lot, you need to unwind any process that used the incorrect lot or else item tracing will forever make it appear like the incorrect lot was consumed as part of the process. This can be a bit tedious depending on how many steps need to be undone, but completely removing the incorrect lot from production outputs is a better case than have your item tracing be wrong in the event that you need to use item tracing for QA purposes or, worse, a recall. I would recommend running incorrect purchase orders through a test environment to understand all the steps and paying close attention to all the ledger entries and results in item tracing.
——————————
Ian Ray
Cypress Grove Chevre
Arcata CA
————————————————————————-
DSC Communities replied 7 years, 8 months ago 1 Member · 0 Replies -
-
0 Replies
Sorry, there were no replies found.
The discussion ‘Lot no. changes’ is closed to new replies.