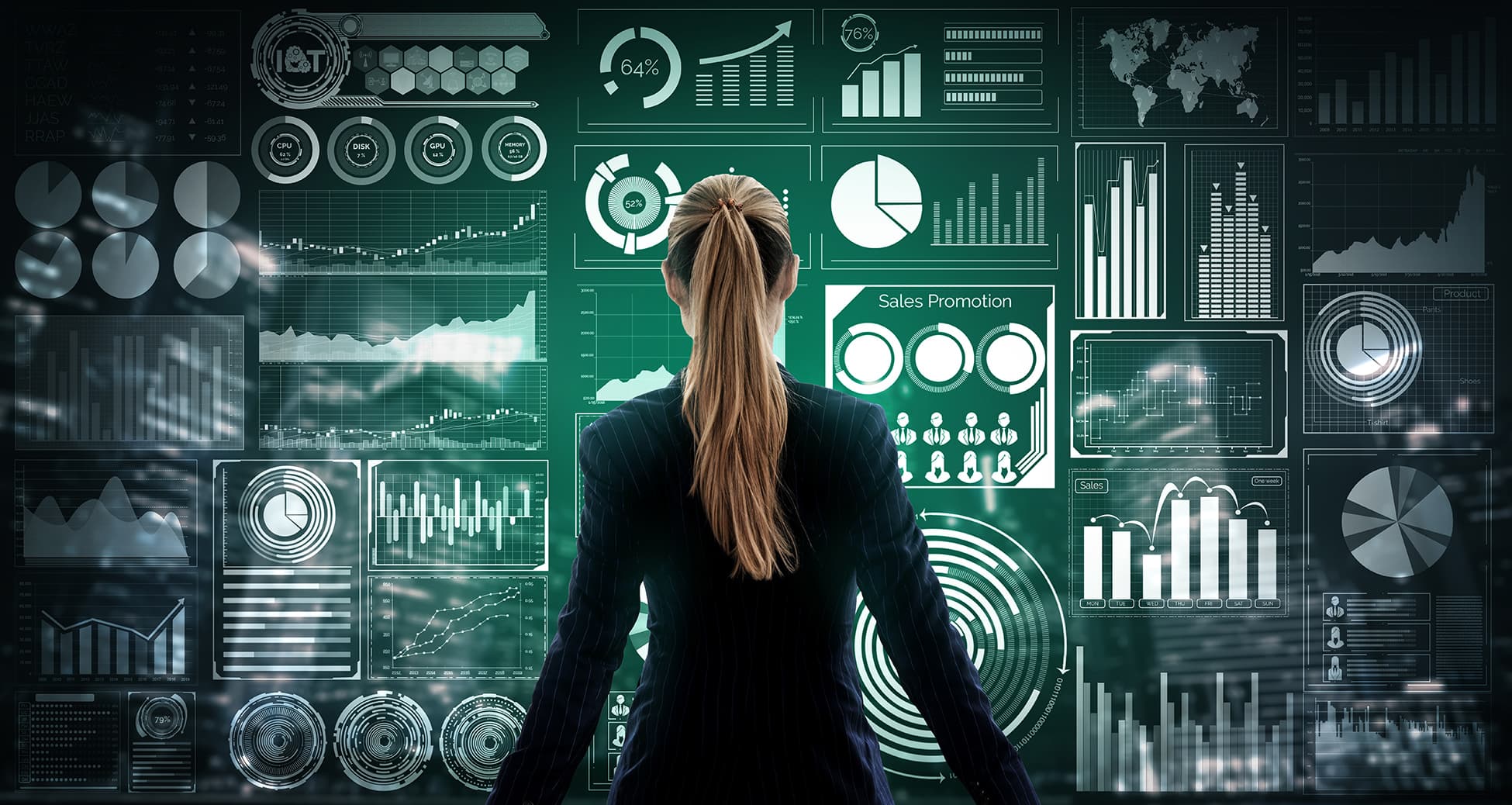
Stock received not invoiced
-
Stock received not invoiced
Posted by DSC Communities on January 10, 2017 at 8:04 am-
Chris Nichols
MemberJanuary 10, 2017 at 8:04 AM
Hi All
Need some ideas in the best way to handle this current issue.
The scenario is as follows
We order goods from a supplier which are free of charge goods as we have paid for the items upfront. The supplier then stores the items on our behalf and we then order as we need for drop shipment to our customer.
When we order these items they are generally ordered drop shipment via a back to back order method and the cost coming back from the supplier is 0.02.
The goods are receipted into the system at 0.02p each. However the po will never be invoiced.
The issue I have is that the Stock received not invoiced will continue to rise, what is the most efficient way to reconcile this purchase receipts in order to remove from the stock received not invoiced report.
Any ideas welcome
thanks
——————————
Chris Nichols
Dynamics Consultant
Vow Europe Limited
Cambridge
—————————— -
If I am understanding this correctly, you order product from your Vendor. They invoice you for the product, but you don’t actually receive the product, it remains with the Vendor. You then place secondary orders with the Vendor to have them ship the product to your customer’s location.
Based on this assumption here is my humble suggestion, the first PO would be to purchase the Inventory to a Location setup for the Vendor. This way you can receive the product to their Location and see a Quantity on Hand at their warehouse. This PO would be closed out by receiving the product (to the Vendor’s Location) and processing the payment/pre-payment.
You would then issue a second PO to the Vendor for the drop shipment of the product to your client’s Ship-To Address. Since you’ve already paid for the product, the cost will be reduced down to whatever their charge is for the drop-shipment. This isn’t very clean in terms of the cost of the product, so hopefully someone can share some tips on helping with this aspect. It wouldn’t be hard to adjust the cost of the product when the PO is marked as a drop-shipment.
Hopefully you’ll be using the drop-shipment capabilities in NAV to help automate the second half of the process.
Best Regards,
——————————
Ben Baxter
Consultant
Accent Software, Inc.
Carmel IN
————————————————————————- -
Eduardo Diaz
MemberJanuary 10, 2017 at 10:20 AM
Hi Chris,
I agree with Ben. You need to create POs to a new location (your vendor’s location) and use prepayments. This will give you better inventory transparency. You will then create Dropship Sales Orders to automatically deplete the inventory. If cost is different by location and you need to track it, make sure to set Average Cost Calculation = Item & Location under the Inventory Setup. As always, run this scenario on a test environment.
Cheers,
——————————
Eduardo Diaz
IT Director
Minequip Corp.
Miami FL
————————————————————————- -
The recommendations provided are good but I feel they have missed a few important details. 1) For the original PO, you received a quantity into inventory to a vendor location and there was mention of payment/prepayment. Just a note that eventually this PO has to be received and invoiced to complete the inventory transaction costing accurately. You cannot leave this received and not invoiced or received and prepaid. 2) This product is never received into your inventory but by processing the receipt, you have a quantity on hand, somehow this quantity has to be reduced by the shipments for the day, week or month. 3) If your dropship POs are being processed at zero dollars for the product, your cost on those sales transactions will be incorrect. Your costs are sitting in inventory from #2 above. 4) There are accounting implications with the handling of both POs that need to be worked through.
May I ask why process the second PO? I would assume it is to provide the vendor with instructions for shipping. And its understandable that the drop ship feature in NAV works nicely for this. However, It seems that maybe a document/report that comes from the sales order instructing the vendor about the shipment, might eliminate the extra work in tracking inventory twice. If not using the second PO would work, you could ship the sales order out of the vendor location from the original PO. This vendor location could also be used as the filter for the report to send to the vendor for shipping instructions. The accounting for this would also be much cleaner and more accurate.
Always more than one way to get your desired results.
——————————
Kim Dallefeld
NAV Consultant
Ft Worth, TX
Kim@Dallefeld.com
————————————————————————- -
Chris Nichols
MemberJanuary 11, 2017 at 3:42 AM
Hi all
Many thanks for your thoughts and comments. Some great feedback
To add some further detail. The original PO will be ordered from one supplier but delivered to the supplier who holds the stock, so when we are advised that the ordered stock is in their warehouse we will then post that original PO.
The item is then set to a consignment item, so that when we order it through a drop shipment it also makes a negative adjustment to the stock through a journal line (automatically) therefore reducing the stock down.
The sales order has a cost of the item for the customer, the PO will have the same cost but when the acknowledgement comes back it overwrites that cost with the 0.02. The reason for the 0.02 is that is the only way supplier can show this item on their system.
So yes we never receive these items into our warehouse, the acknowledgement automatically updates the qty received on the PO and the SO, so we can then invoice the customer. the PO however will never be invoiced from the supplier.
On point 4 from Kim – There are accounting implications with the handling of both POs that need to be worked through. It is this I am trying to solve.
would it be better to get the supplier to invoice us for those goods @0.02 match the PO, receive it and then get a credit amount back? could be one option?
anything else
thanks again
Chris
——————————
Chris Nichols
Dynamics Consultant
Vow Europe Limited
Cambridge
————————————————————————- -
Chris, more thoughts…
1- Do you need to record the .02 from the second PO as cost? If not, then change the cost to zero on that PO at the point that you post the receipt. You will need to invoice this PO but since its zero dollars, there will be no accounting impact.
2 – Apparently you have a modification that is creating a journal to reduce the original PO quantity out of inventory. Though this does update your quantity on hand, a typical negative adjustment debits an inventory adjustment account. You might have this set to cost of goods for normal adjustments. The general ledger account that is used can be changed in the journal with the desired general business posting group/general product posting group combination. You might adjust the mod to pull these values from the PO or associated sales order.
3 – Because of the two POs and the journal entry, I would say that the profit you are seeing on individual sales transactions will not be accurate but your general ledger should reflect good numbers if you adjust the posting setups as necessary.
If I can help you more specifically, send me an email.
——————————
Kim Dallefeld
NAV Consultant
Ft Worth, TX
Kim@Dallefeld.com
————————————————————————- -
Jason Nicolaou
MemberJanuary 11, 2017 at 7:34 AM
Kim you make an excellent point. These are all great options!
As a user I implemented an arrangement like this in a manufacturing environment where scrap was not consistent so the raw material had to be flushed manually. It was much cleaner and more accurate for us to simply set up a subcontractor location and consumes form that location. As long as your G/L is mapped to the same accounts as the material in your primary location, then everything (PO’s, SO’s, costs, etc.) will roll up accordingly. In fact you gain greater visibility because an additional filter (location) has just been added to the transactions.
Please report back what you implement and how well it worked. This is an interesting scenario.
Good luck!
——————————
Jason Nicolaou
Solutions Architect
Socius
Dublin OH
————————————————————————- -
I’m thinking that the 2nd PO cannot be for the item itself or you will increase your inventory when you receive this item, since the inventory was previously received and paid for. If you want this handling charge assigned to the item, you would need to do a PO with a Charge(Item) line on it for extra charge. Unfortunately, the standard drop shipment process does not create Charge(Item) lines on a PO. Additionally, the Charge(Item) would spread the cost over all the inventory previously received and not just the items sold on a particular sales order.
An alternative would be to setup the vendor location as the storage location for the inventory as mentioned previously. Then, create a virtual location as the pass through for the sales orders. The virtual location would also have a stockkeeping unit set up such that the replenishment method for the virtual location would be a transfer order from the vendor location. When sales orders are received, the location on the sales order would be the virtual location. This would create demand at the virtual location. The replenishment worksheet would then suggest a transfer order from the vendor location to fill the order. The transfer order would be the document the vendor would use to fulfill the order. Some customization would be need to pass the ship to information from the sales order to the transfer order so the vendor would ship to the correct customer.
When the vendor invoice for the handling is processed, it would be entered as a Charge(Item) and applied to the transfer receipt at the virtual location. This would apply that charge to only that receipt and not all the inventory at the vendor location. This would also require that the transfer order gets shipped and received first, and then the sales order would get processed.
This would allow tracking of the sales order back to the vendor as well as maintaining proper costing of the inventory through to the sales order. A little tricky, but may provide an alternative.
——————————
Dave Wiser
Controller
Beckwith & Kuffel
Seattle WA
————————————————————————- -
Can you treat the supplier as a location?
From what you said, the invoice never gets paid because you already paid up front. I assume that they send the invoice with the .02 because their system won’t allow 0.00.
——————————
Ron Ketterling
President
Business Automation Specialists of MN, Inc.
Minneapolis MN
————————————————————————- -
Usually the $0.02 (or similar) charge is for handling the product and preparing it for shipment. I previously work for a company that did the same thing. The vendor stored our product and then charged a handling fee to package it up and ship it.
——————————
Dave Wiser
Controller
Beckwith & Kuffel
Seattle WA
————————————————————————- -
Chris Nichols
MemberJanuary 12, 2017 at 9:42 AM
Hi Allthanks for all the effort and input and great to get some different options.
After further consideration I think the best option in the short term is to update the PO price to a zero value and then post the invoice.
We will continue to investigate a more automated solution
Chris
——————————
Chris Nichols
Dynamics Consultant
Vow Europe Limited
Cambridge
——————————
——————————————- -
Michelle Berry
MemberJanuary 13, 2017 at 9:28 AM
Chris –Do you need to use the PO?
_If the answer is no, then simply do positive inventory adjustments. If you need them to track outstanding orders, you can enter the PO’s and just delete the PO’s as they come in and inventory adjs can get the inventory in the system.
If critical to track inventory movement with PO:
_Enter PO with .02 ea and actually invoice the PO once completed, do a neg GL line to write off the invoice so it creates a $0 invoice to whatever GL account they want to recognize it in. If they are holding an inventory value of .02 ea, they have to recognize it somewhere, so a simple GL write off entry on the same Purchase invoice is best and easiest for any auditing to understand. This clears the issue of the rcvd-not invoiced and negates any incorrect AP balances.
If not critical to track inventory movement on PO, but still want PO for planning:
_If they don’t want to invoice they can do positive inventory adjustments instead of receiving against PO and manually adjust those quantities down on the PO if they need to keep the PO process in place.
Michelle
——————————
Michelle Berry
NAV Advisory Consultant, Director of Sales NA
NAV DNA, LLC
Clearwater FL
——————————
——————————————- -
Jamie Theis
MemberJanuary 16, 2017 at 7:34 AM
Chris,
If you are paying for the items up front you could use the Prepayment option in the PO to pay for original invoice and as they come in you would receive them into inventory. I would run this in your test company to make sure that works to your satisfaction before using it in the live NAV. This way you could test it all the way through from opening the PO, to Invoicing the Prepayment at 100% cost, Receiving the items, a finalized invoicing to clear the PO.
I have never done a Prepayment like this so I am not sure how much NAV will like the Prepayment at 100% and how it will react after you receive the Items and post the Invoice to close out the PO, just as a warning. But if it does work this way it will keep costing and inventory correct without having to do much more work.
——————————
Jamie Theis
Purchasing Manager
Hewitt Docks, Lifts & Pontoon Legs
Nicollet MN
——————————
——————————————- -
Chris Nichols
MemberJanuary 16, 2017 at 11:31 AM
Thanks Michelledue to a mod we have created the PO’s are drop shipments and automatically updated based on the acknowledgements received from the supplier. These PO’s are linked to an SO, so couldn’t just delete unfortunately as that would be an option.
but I do like the option number 2 which I will look at further.
thanks for your help
Chris
——————————
Chris Nichols
Dynamics Consultant
Vow Europe Limited
Cambridge
——————————
——————————————-
DSC Communities replied 7 years, 4 months ago 1 Member · 0 Replies -
-
0 Replies
Sorry, there were no replies found.
The discussion ‘Stock received not invoiced’ is closed to new replies.