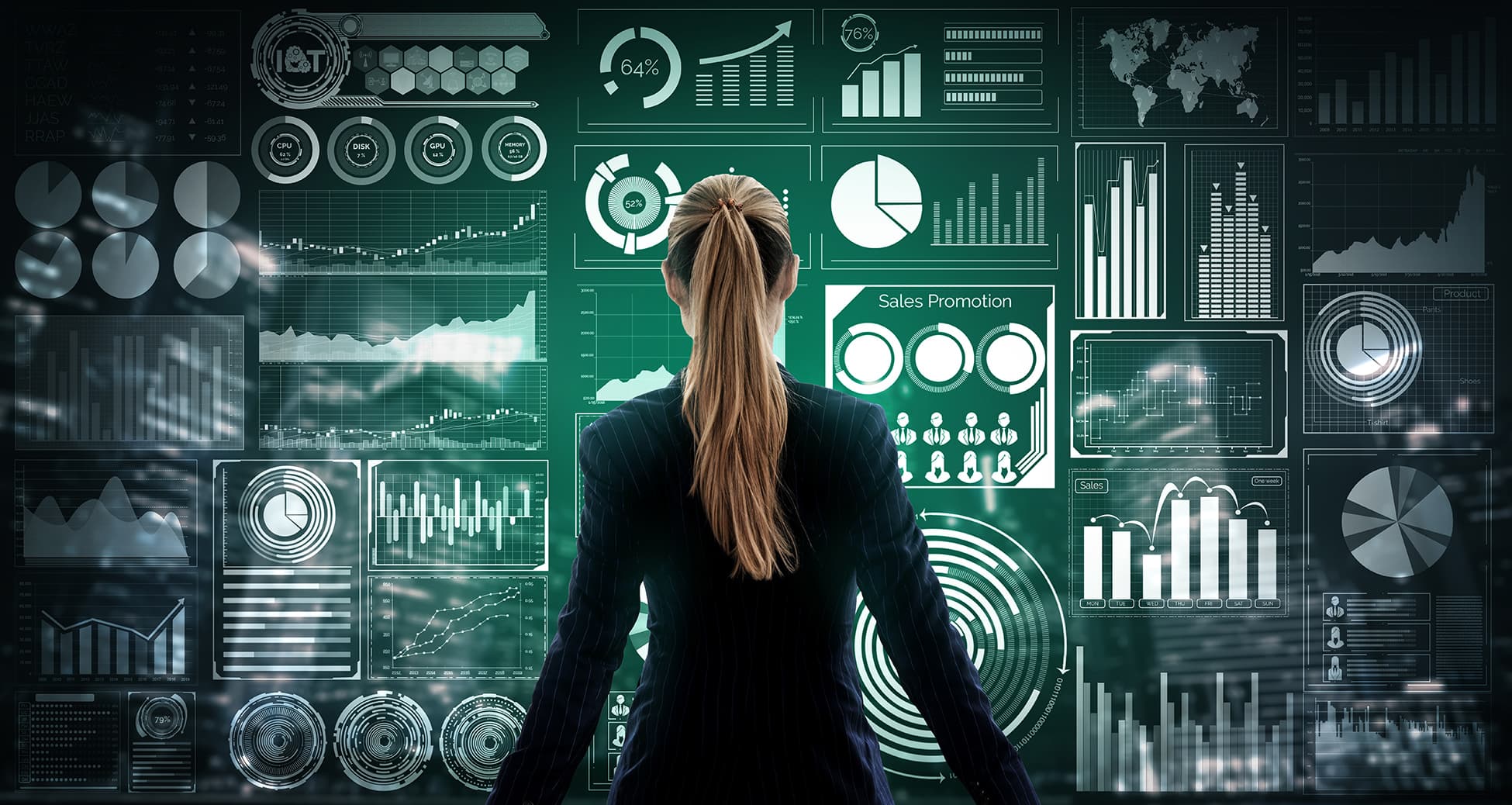
MRP’s impact on Item Availability by Timeline
-
MRP’s impact on Item Availability by Timeline
Posted by DSC Communities on January 10, 2017 at 1:45 pm-
Daniel Rock
MemberJanuary 10, 2017 at 1:45 PM
Hi everyone, first time poster!
I have been working on setting up MRP, and my biggest concern is how this will impact the Item Availability by Timeline.
We are needing to set up each SKU to maintain a specific number of weeks of supply in each of our locations — a week of supply may vary depending on the time of year, so we would need for this to be dynamic.
I think the best setup for us on each SKU card is to use a “Lot-for-Lot” reordering policy and also inputting a Safety Lead Time,
The problem I’m running into with using a safety lead time is that it artificially pushes back the expected receipt date by that set amount of time. On the timeline, this is visually deceiving and confusing.
Is there any way to have the Item Availability by Timeline utilize “Planned Receipt Date” instead of “Expected Receipt Date”?
I have also explored using a “Fixed Reorder Qty” policy as this would give us an accurate portrayal of our expected receipts, but this would require us to manually update the reorder point on each SKU every time our forecast changes, and this would be cumbersome.
Thanks so much in advance for your help!
——————————
Daniel Rock
The Fishin’ Company
Rogers, AR——————————
-
Jason Nicolaou
MemberJanuary 11, 2017 at 7:26 AM
Hi Daniel welcome to the group!
There is logic behind the “Planned Receipt Date” and the “Expected Receipt Date” so before making the change you may want to research the impact of changing where these are pointed.
Now to answer your question, my advice is to not try to outsmart NAV. It is structured in a way that works for many businesses. How did you determine that the Safety Lead Time is the best setup? It is helpful to share you logic here. At its simplest form, you want your folks to be able to see when the material will be in hand so I don’t understand how the safety lead time causes confusion. Another option may be to increase the warehouse handling time because you can adjust per location.
Hopefully this was helpful. Once again, welcome and thanks for submitting the interesting question.
——————————
Jason Nicolaou
Solutions Architect
Socius
Dublin OH
————————————————————————- -
Rick Dill
MemberJanuary 11, 2017 at 11:24 AM
HI Daniel;
There is a lot here to discuss. While I don’t really try to push product solutions, your desire to carry X days of inventory in stock, and have it dynamically changed can’t really be handled by either lot for lot or reorder point.
Lot for lots goal is to drive inventory to zero in a given period based on demand. You then use safety stock to make sure you have inventory to cover deviation from plan. You would have to adjust safety stock on a “daily” bases in the lot for lot planning as well.
There is an add-on product called AFP. AFP actually plans to number of days stock, and that stock level is driven by “Forecast/demand”.
This sounds like what you are trying to do.
——————————
Rick Dill
Consultant
ArcherPoint Inc.
Waupaca WI
————————————————————————- -
I’m also a big fan of not trying to outsmart the NAV engine. If you think of the NAV Customer base being 100k+ companies, it generally has to have an MRP engine that works.
With that being said, I agree Lot-for-Lot does not allow you to keep a set amount of Inventory on Hand. Lot-for-Lot is aimed at lean inventory levels, while still allowing for volume discount ordering. If you don’t need a specific quantity on hand, then the Lot-for-Lot policy sounds like a good fit.
Have you considered building an import to the Forecasting module? This way you’re planning can reflect current projections based on your forecast. If you import a new forecast, the MRP suggestions will change. This strategy really only works if you are being fed the forecast numbers from Customers. Otherwise you’re simply moving the manual process of updating the stock levels to Excel, prior to import.
——————————
Ben Baxter
Consultant
Accent Software, Inc.
Carmel IN
——————————
——————————————-
DSC Communities replied 7 years, 4 months ago 1 Member · 0 Replies -
-
0 Replies
Sorry, there were no replies found.
The discussion ‘MRP’s impact on Item Availability by Timeline’ is closed to new replies.